PVC 1220 single color foaming back or calender back coil mat production line
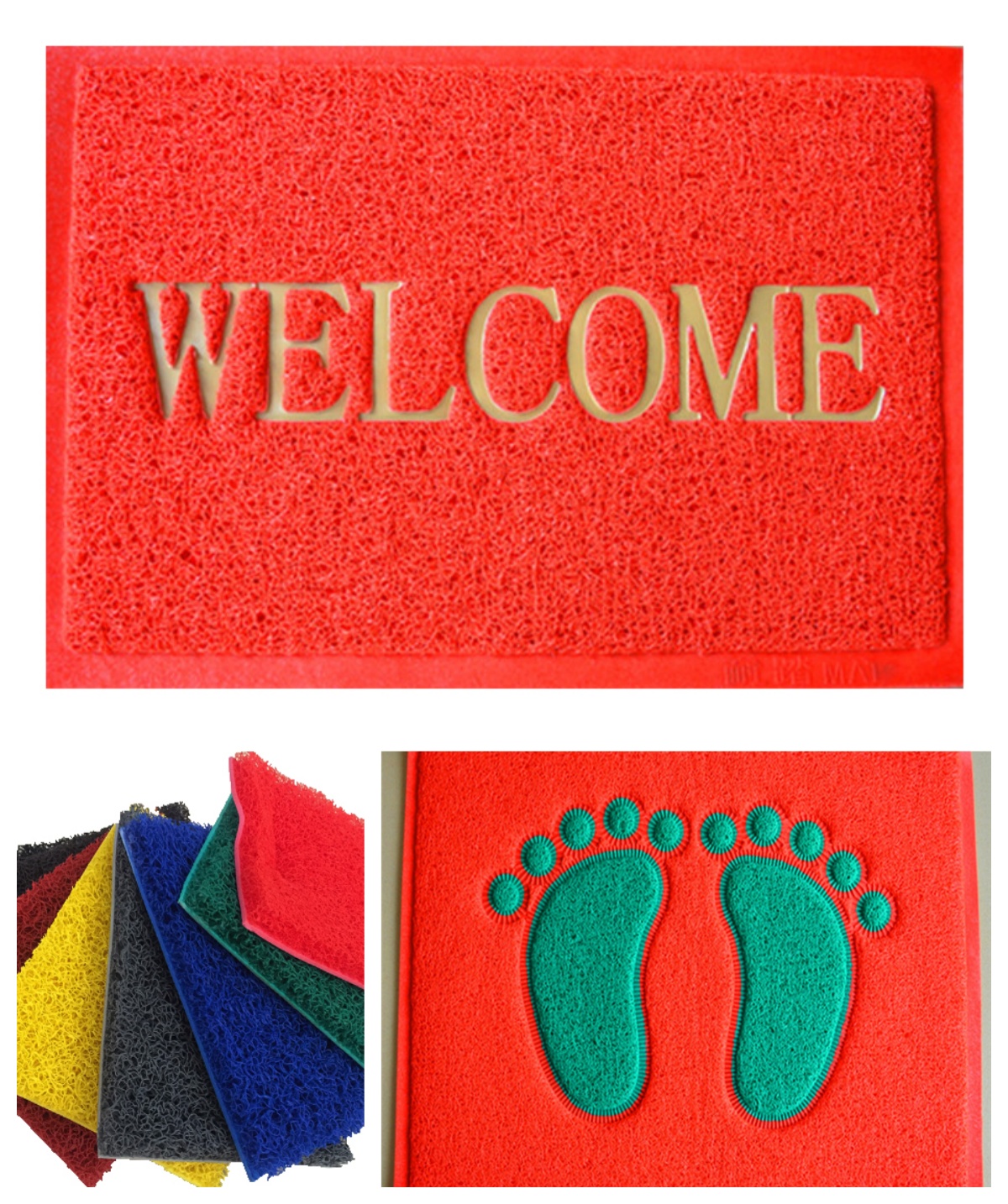
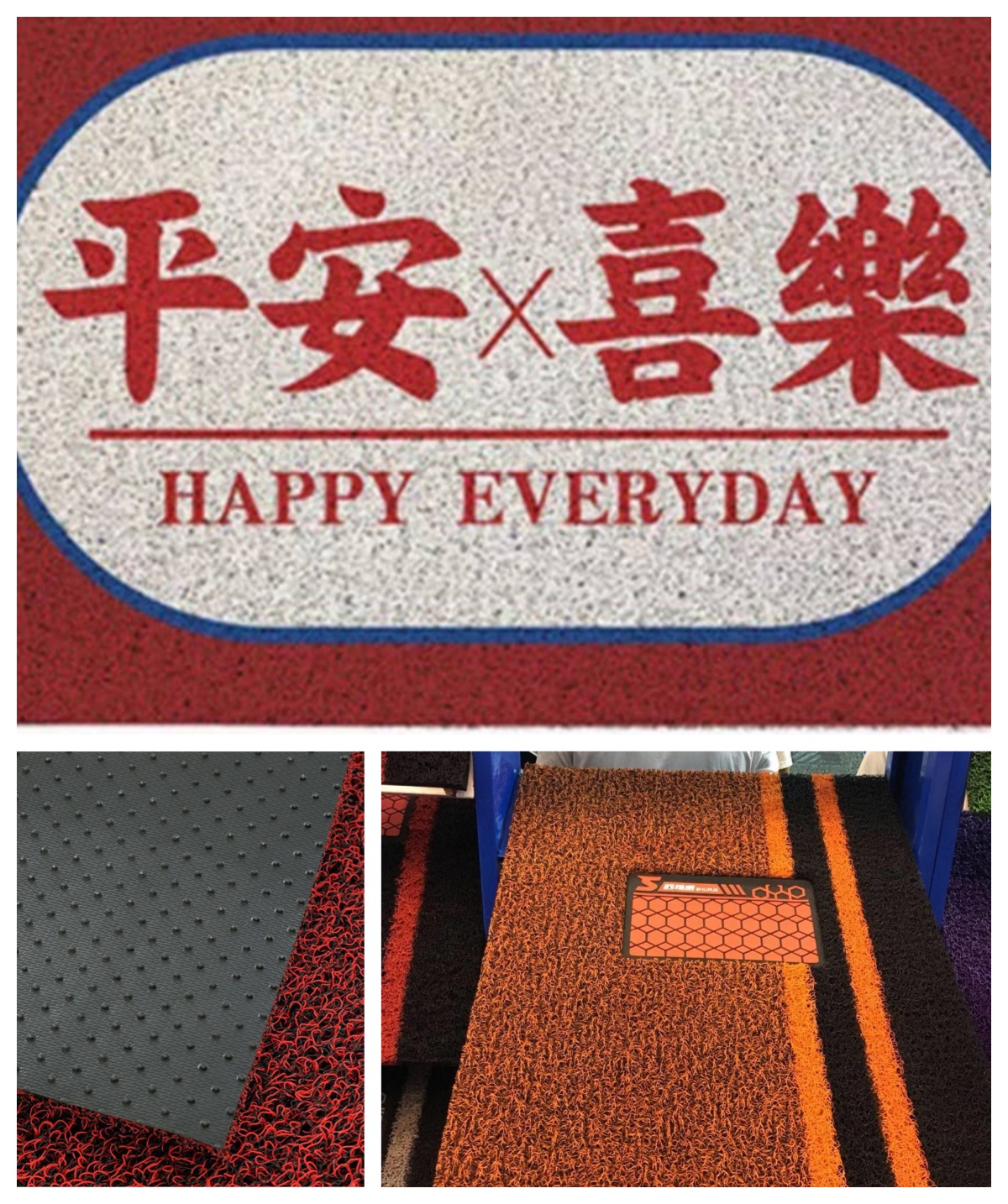
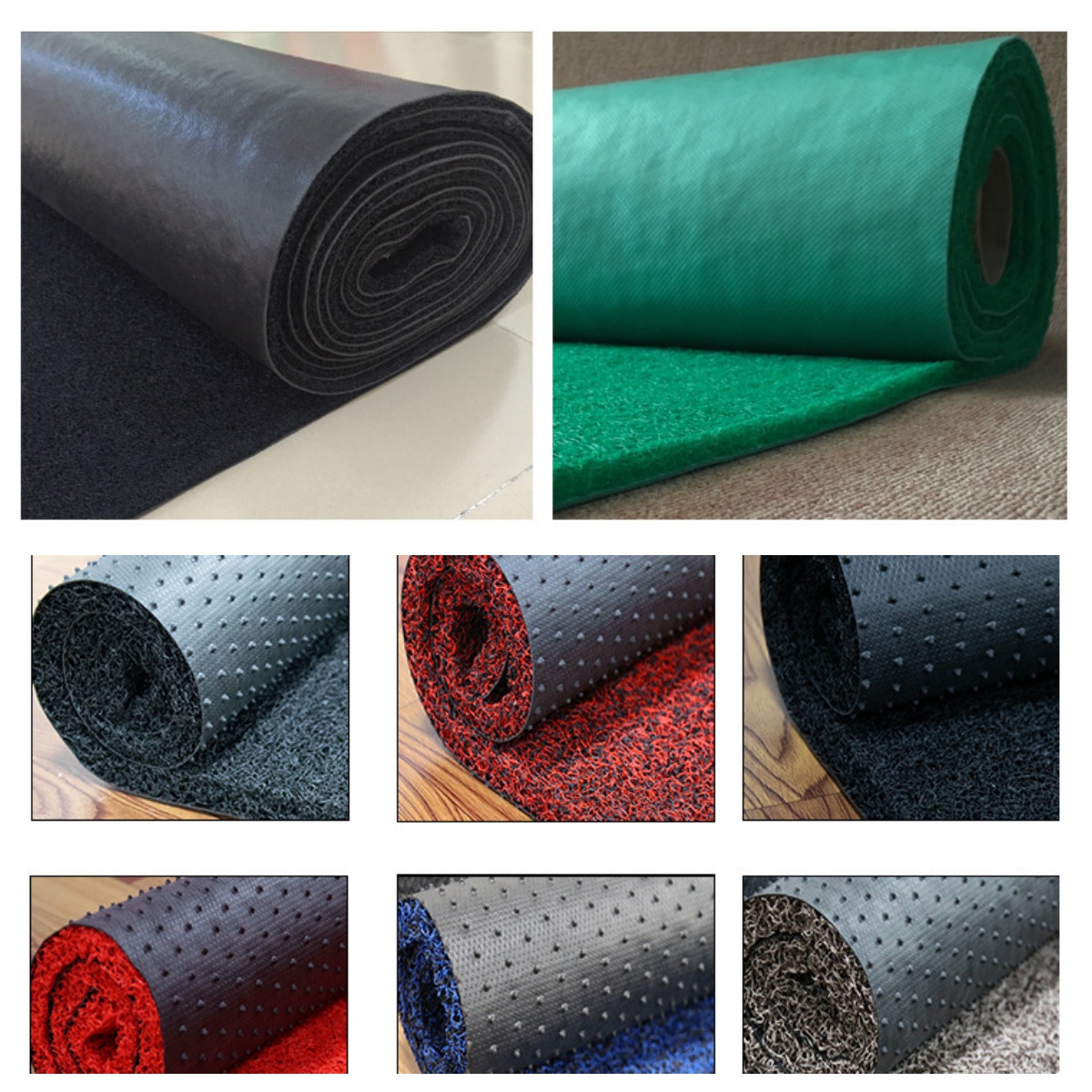
PVC Cushion Floor Mat Production Line (Modular Configuration)
1. Extrusion System
- Filament Extruder: Melts PVC raw materials at high temperatures for filament formation. Equipped with hyperbolic nozzles to control melt shear velocity.
- Sheet Extruder: Produces PVC substrate for the mat backing. Select models support twin-color filament synchronous extrusion.
- Auxiliary Units: Hydraulic screen changer (for impurity filtration), forced feeding system (ensures uniform material flow).
2. Molding & Setting System
- Rotating Mold: Controls filament density and pattern geometry.
- Cooling Unit: Utilizes water bath immersion setting or roller-air cooling to stabilize filament structure.
- Coating/Impregnating Device: Enhances adhesion strength between filaments and substrate layer.
3. Post-Processing System
- Haul-Off Unit: Adjusts conveying speed to prevent deformation.
- Cutting & Rewinding Machine: Automates trimming and rolling functions. Supports custom sizing (e.g., elevator mats, promotional mats).
A |
Extrusion machine |
|
B |
Mould |
1 SET |
C |
Wire forming machine |
1 SET
|
D |
Water flapping machine |
1 SET
|
E |
Wire conveying machine
|
1 SET
|
F |
Backing molding machine |
1 SET
|
G |
6.2-meter dryer
|
1 SET
|
H |
Wire glue dipping and pasting device |
1 SET
|
I |
Hot air circulation duplicate re-shaping box |
1 SET
|
J |
Tractor |
1 SET
|
K |
Bead cutter |
1 SET |
L |
Length measurer |
1 SET |
M |
Coiler |
1 SET |
Auxiliary Equipment:
200 -High speed mixing machine * 1 set
360-crusher *1 set
Sincerely look forward to receving your inquiry and cooperation in long-term!
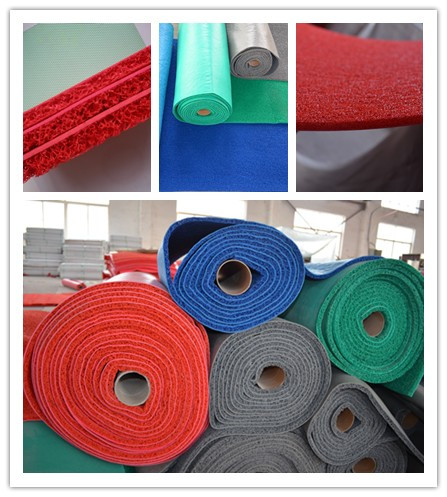
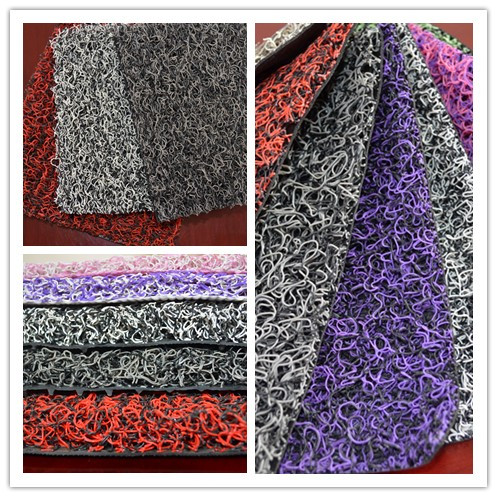
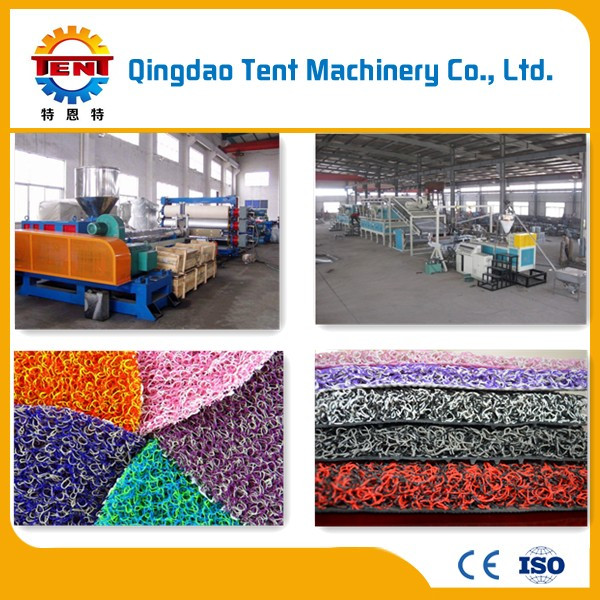
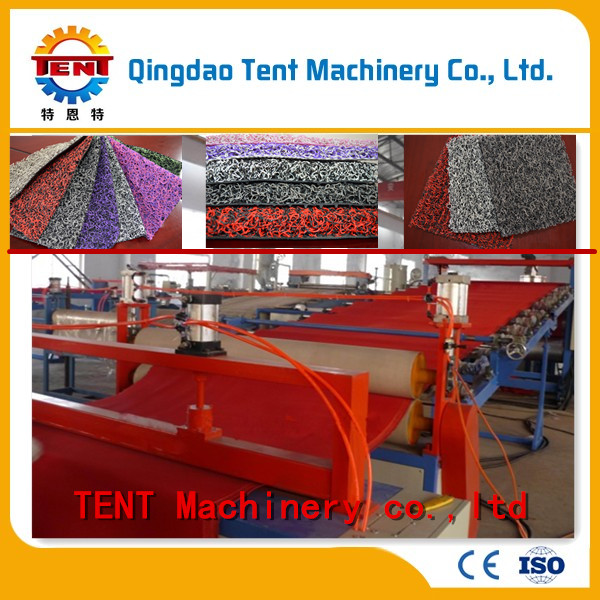
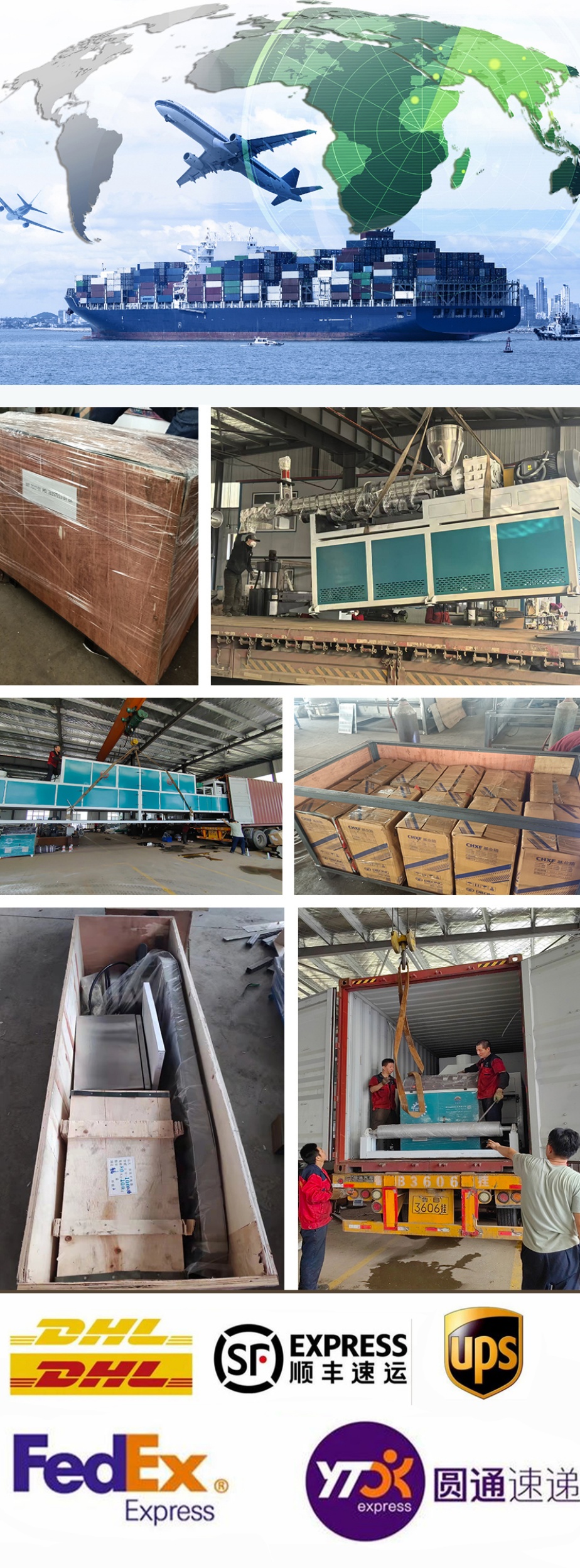
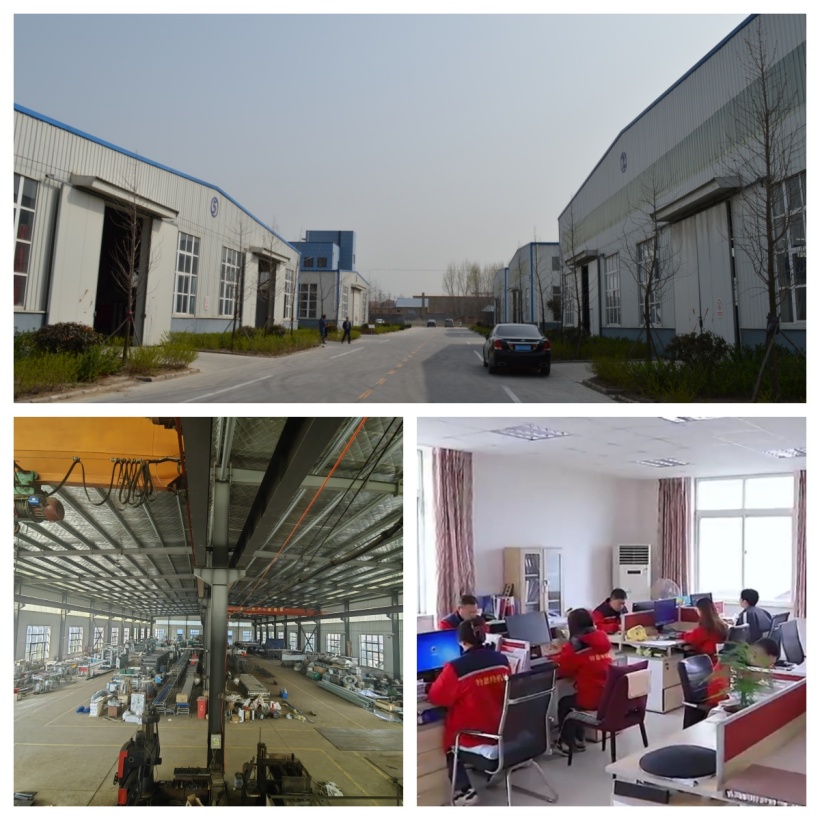
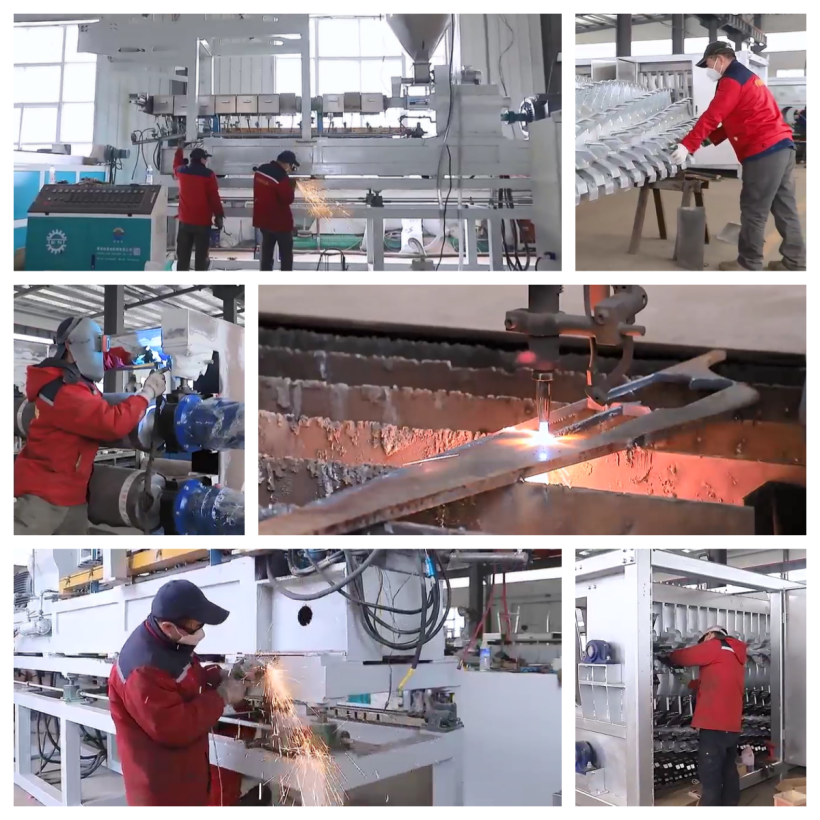
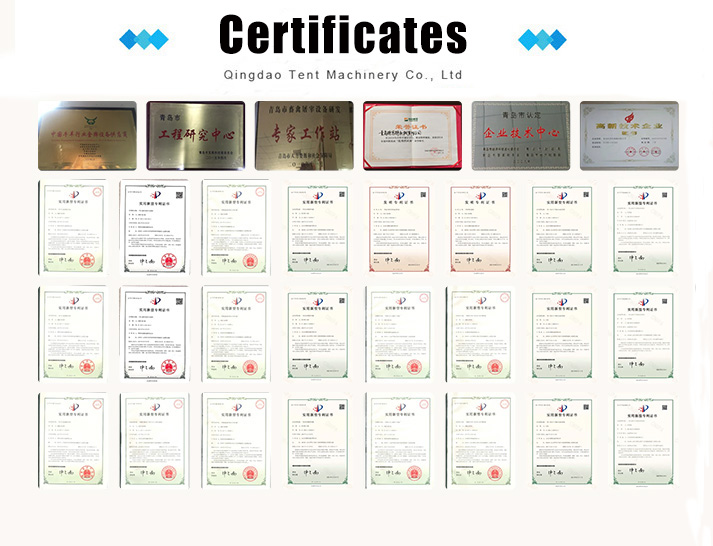
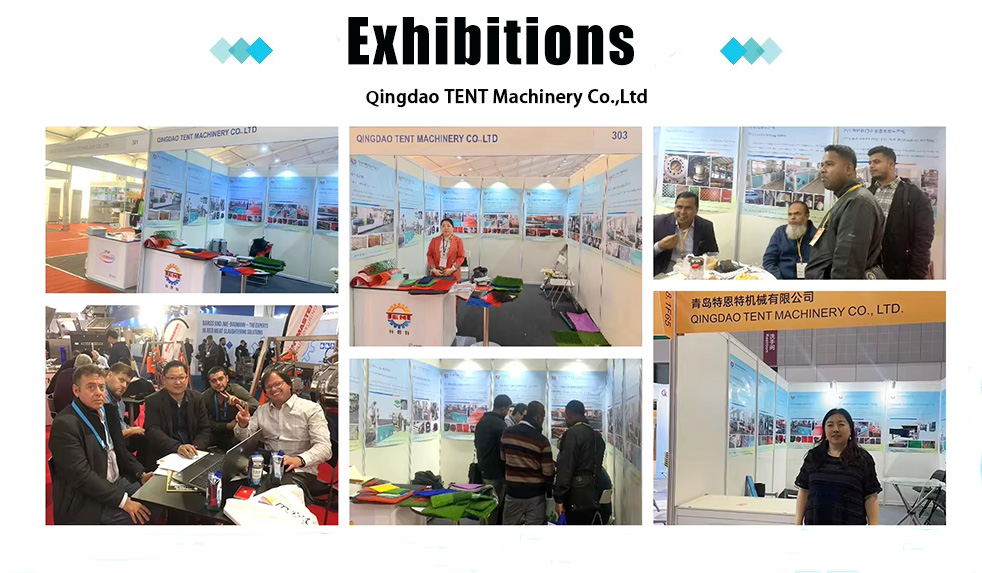
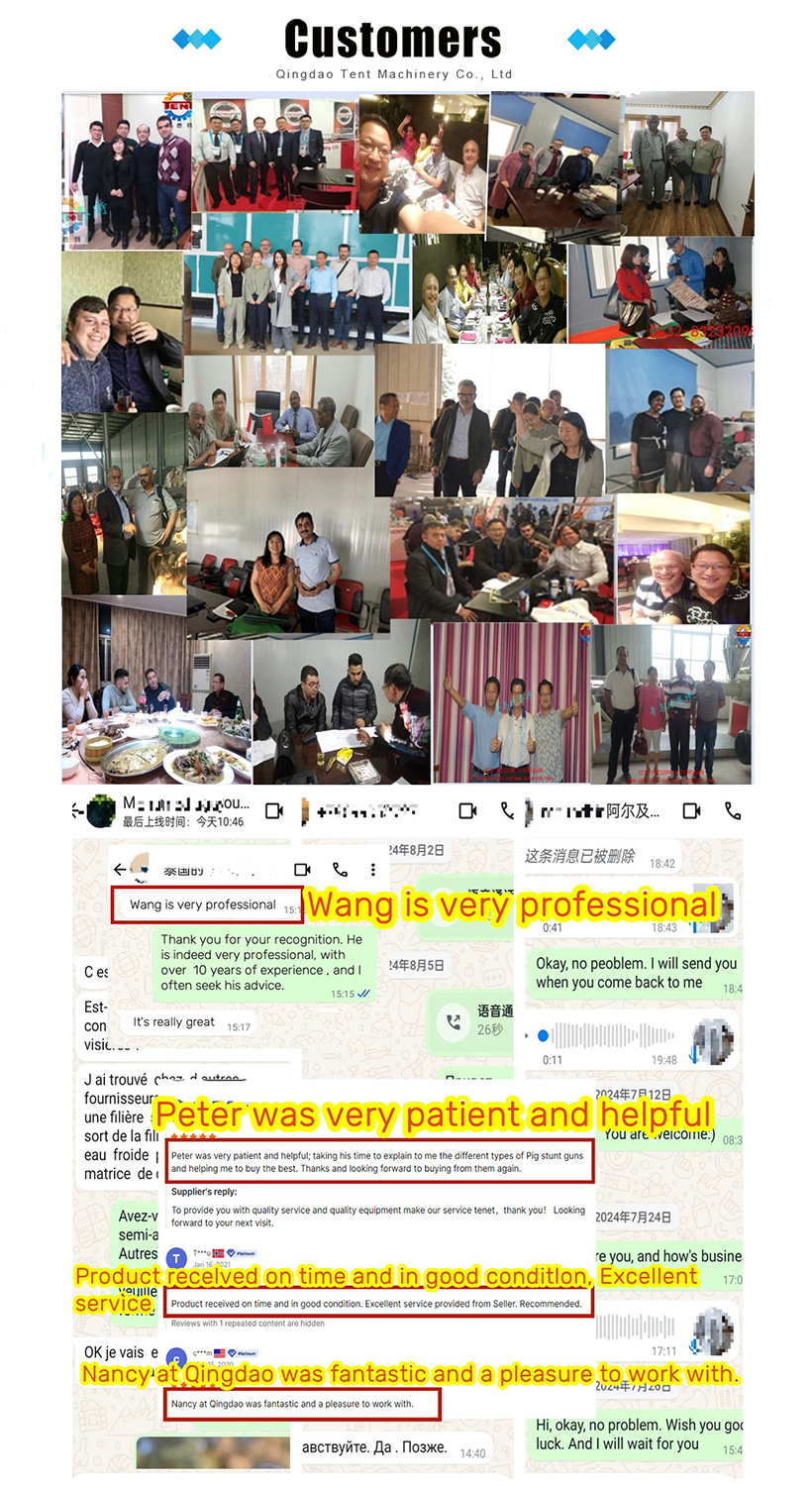