MetalInjectionMolding (MIM) is will modern plastic injection forming technology into the field of powder metallurgy and the formation of a new metal parts near net shape forming technology, in recent years, powder metallurgy disciplines and industrial sectors in developing very rapidly in a new and high technology. The process is: first solid powder and organic binder is mixed uniformly practice, after pelletization in heating plasticized by injection molding machine injection mold cavity curing forming, then using chemical or thermal decomposition method will be forming in casting binder removal, the Sintering Densification by the final product.
MIM technology in the preparation of three-dimensional complex geometry, uniform structure and high performance of the near net shape products has a unique advantage, as follows:
1 can be like the production of plastic products, the production of a complex shape metal parts.
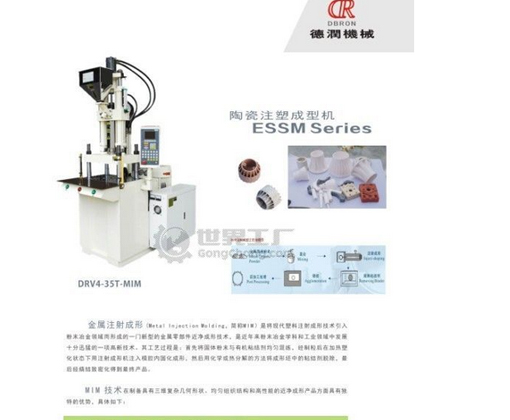
2 low cost of products, good finish, high precision (+ 0.3% ~ + 0.1%), generally do not require subsequent processing.
3 product strength, hardness, elongation and other mechanical properties such as high mechanical properties, good wear resistance, fatigue resistance, uniform organization.
4 the raw material utilization rate is high, the production automation degree is high, the working procedure is simple, but the continuous mass production.
In order to simplify the production process of ceramic products, Derun company in order to simplify the production process of ceramic products, but also improve the production efficiency of ceramic products. The Derun company specially designed ceramic kitchenware, ceramic peeler for injection molding machine.
Ceramic product forming step:
The first step: mixing, the ceramic powder and binder in accordance with a certain proportion of mixed together. To make the material flow.
The second step: injection molding, with the flow of the material, the use of injection molding machine injection molding.
The third step: skim, the product inside the binder removed, for the back of sintering, increase the hardness of the product and finish to prepare.
The fourth step: sintering, the temperature of 1700 degrees, in the sintering furnace sintering products, so that the product has enough hardness and strength.
Ceramic hot kitchenware vertical injection molding machine, ceramic molding machine, ceramic injection molding machine, vertical injection molding machine special for ceramic, ceramic injection molding machine, ceramic powder injection molding machine, tungsten steel sheet injection molding machine, tungsten powder molding machine, zirconia injection molding machine, alumina injection molding machine (15T~650T)
Ceramic forming machine for vertical injection machine special for ceramics
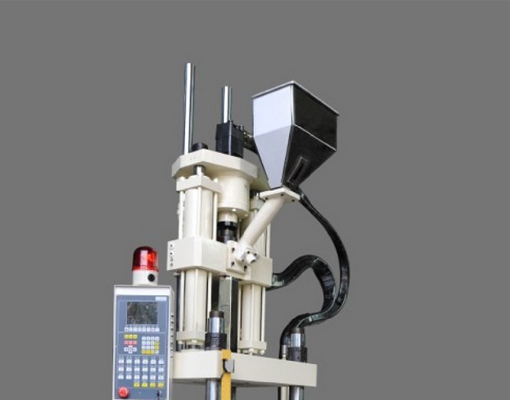
1, ceramic machine (standard machine series 15T ~ 450T)
2, ceramic machine (single slide series 25T ~ 450T)
3, ceramic special machine (double slide series 25T ~ 450T)
4, ceramic special machine (disc machine series 55T ~ 450T)
5, ceramic machine (vertical horizontal series 55T~650T)
Suitable for manufacturing ceramic steam turbine components, auto parts, diesel engine parts, electrical switches, home appliance parts, watches parts, ceramic decorations, etc.. In addition to the production of the company's vertical injection molding machine for alumina, zirconia, silicon carbide and other ceramic materials, but also for the manufacture of powder metallurgy parts. Injection molding is a porcelain powder and organic binder, the injection molding machine, in 130~300 temperatures will ceramic material is injected into the mold cavity, cooling, curing of the adhesive can remove the sintering the blank and forming. The injection molding method can be used to form complex products, the blank size and the actual size of the sintering after the high precision, size tolerance within 1%.
Ceramic powder injection molding (CeramicInjectionMolding) is a new type of ceramic powder injection molding technology, which requires high precision ceramic parts. Injection molding technology of ceramic powder material is another kind of precision injection molding technology in addition to traditional hot pressing and hot pressing. In recent years, the application fields of injection molding parts mainly include automobile, electronics, petroleum, textile, magnet production, clock and watch, household goods, medical technology and so on.
Benefits of injection molding of ceramic powder materials include:
- mass production
The use of traditional craft production parts can be completed in one step production
The design and implementation of complex shaped parts
It can quickly adjust the production
The high surface quality of molding parts
The molding parts with high dimensional stability
Re - processing parts without time-consuming and expensive
The selection of the manipulator can automatic production
Injection molding and injection molding method, also known as injection molding. General injection molding method is the will of the components of the polymer pellets into the charging barrel of injection molding machine, after heating, compression, shearing, mixing and transport effect, make the material and melting, this process also known as plasticization. Then with the aid of plunger or screw to the melted polymer melt pressure, high temperature melt by material in front of the tube nozzle and mold runner system of injection advance closure of low temperature in the cavity, and the cooling shaping can open mold, ejection products, has a certain geometry and precision of plastic products, after high temperature dewaxing and sintering the ideal products
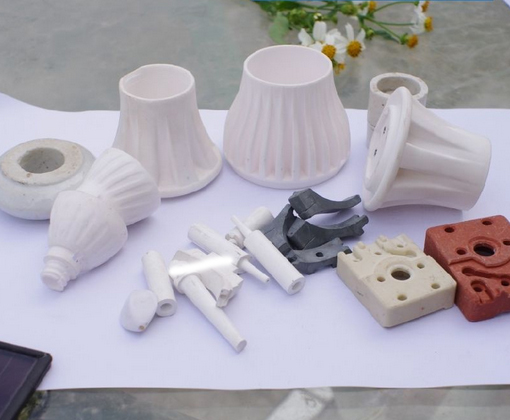